technology
Overview
·The FXZ series scrap steel preheating and conveying equipment is a complete set of equipment for electric furnaces, designed to preheat furnace charge using waste heat from the furnace. This ensures stable molten pool conditions, shortens the smelting cycle, and enables continuous feeding of scrap steel into the electric furnace through its four openings. Additionally, it leverages the electric furnace’s high energy efficiency to save both electrical and chemical energy, improve working conditions, and achieve clean, energy-efficient, and high-efficiency steelmaking.
·The FXZ series scrap steel preheating and conveying system serves as the raw material conveying system between the scrap steel yard and the electric furnace. Its primary function is to utilize the residual heat from the electric furnace to continuously preheat scrap steel within the FXZ material hopper and feed it into the furnace. This equipment employs a series of advanced technologies, including electric furnace flue gas residual heat recovery and utilization, scrap steel preheating and conveying, high-temperature flue dust purification, and other advanced technologies to effectively address issues such as high energy consumption, low production efficiency, and severe environmental pollution in electric furnace production. It achieves innovative metallurgical processes featuring continuous scrap steel conveying, continuous preheating, continuous melting, fully enclosed, full-cycle, and full-melting-pool operations. 更改此文本。
Process Features
. To ensure uniform preheating of scrap steel entering the feed hopper, the conveyor continuously performs horizontal reciprocating vibrations, causing the scrap steel within the hopper to move forward continuously until it is fed into the furnace..
The high-temperature flue gas emitted by the electric furnace flows through the preheating hopper in the opposite direction of scrap steel input..
During continuous scrap steel loading into the electric furnace, the molten steel pool within the furnace remains in a liquid state, with incoming scrap steel directly falling into the molten pool. The arc is heated on the flat molten pool covered with foam slag. The entire process of molten pool oxidation smelting and foam slag operation has changed the traditional electric arc furnace scrap steel smelting process. Under these conditions, the arc remains stable, significantly reducing the reactive power impact on the power grid caused by the three-phase current during the scrap steel melting period.
This effectively avoids the impact of the arc’s constant changes on the average input power during traditional electric furnace scrap steel melting, thereby improving the power grid’s safe operation index.
Continuous charging ensures that scrap steel can be fed into the furnace throughout the entire power-on phase. Therefore, there is no need to open the furnace lid, avoiding heat loss caused by opening the lid. Since the furnace lid remains closed, a continuous preheating charging system channel is used to exhaust fumes while simultaneously heating the scrap steel within the channel.
Technical Specifications.
The charging method for electric furnaces using FXZ-type scrap steel preheating conveying equipment has been changed from the traditional method of opening the furnace cover and charging with a basket to a continuous charging method using preheated scrap steel. The electric furnace has achieved “four continuous” fully enclosed high-efficiency smelting, with significant effects in terms of energy saving, emission reduction, and increased production. It has the following characteristics:
The smelting cycle is shortened by 10-15 minutes;
The amount of steel produced per unit time is increased by more than 10%;
Electricity savings of 80-100 kWh per ton of steel;
Electrode consumption reduced by 0.5-0.8%; Refractory material consumption reduced by 5%, with CO2 emissions from steel production reduced by 20-30%;
Steel dust generation reduced from 17-20 kg to 15 kg;
Metal recovery rate increased by 1.5-2%, with an expected recovery rate of ≥90%;.
At the electric furnace feed port, scrap steel can be preheated to over 400°C: reducing grid fluctuations.
Key parameters
Model | Tank Specification (Width) | Leather Bowl Size (Width×Height×Length) | Processing Capacity (t/h) | Electric Furnace Capacity (t) |
---|---|---|---|---|
QSFXZ15 | 1260mm | 500×300×300 | 100 | 15 – 20 |
QSFXZ30 | 1400mm | 700×400×400 | 120 | 20 – 40 |
QSFXZ50 | 1560mm | 800×400×400 | 150 | 40 – 50 |
QSFXZ60 | 1560mm | 800×400×400 | 180 | 50 – 60 |
QSFXZ70 | 1800mm | 1000×500×500 | 200 | 60 – 80 |
QSFXZ80 | 1800mm | 1000×500×500 | 200 | 70 – 90 |
QSFXZ100 | 2000mm | 1100×500×500 | 250 | 80 – 100 |
QSFXZ120 | 2200mm | 1200×500×500 | 300 | 100 – 150 |
Process layout
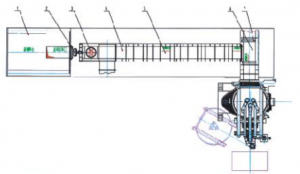
Multi-stage steering type scrap steel preheating conveyor equipment
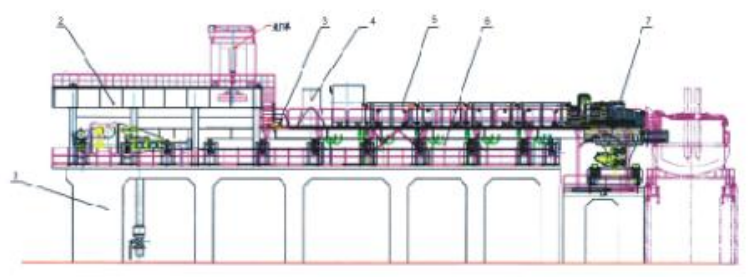
New type of storage-type scrap steel preheating conveying equipment
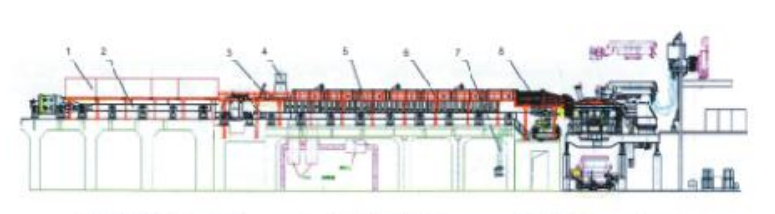
Vibrating conveyor equipment for scrap steel with conduction heating function
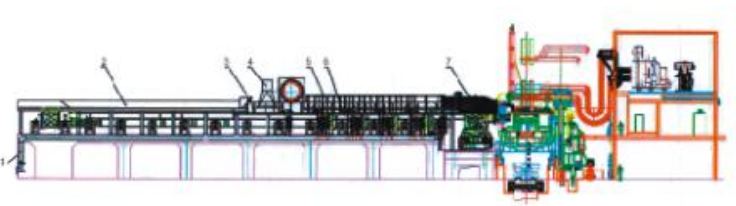
FXZ Series Scrap Steel Preheating and Conveying Equipment